Négoce de profils extrudés, de pièces moulées et tapis en caoutchouc
Avec 40 années d’expérience dans l’industries, F.SIKORSKI Industrie dispose d’un réseau de partenaires industriels exerçants dans différents secteurs d’activités permettant d’offrir à nos propres clients un complément de gamme en étanchéité et produits techniques (profiles extrudés, joints moulés toriques et sur mesure, tapis en caoutchouc).
Nous gérons le développement du produit, le contrôle réception, le stockage et la distribution.
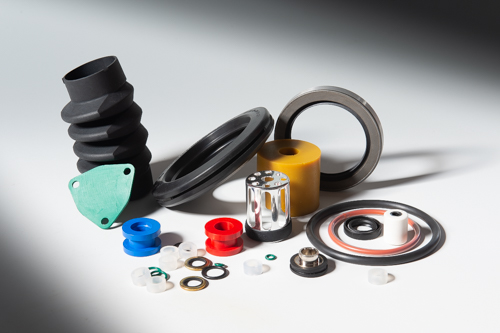
Extrusion de profilés en caoutchouc
L’extrusion du caoutchouc est un procédé largement utilisé pour créer des profils mono ou bi-matière, avec ou sans insertion métallique. Il s’agit d’un processus continu qui extrait le caoutchouc, à l’état malléable, à travers une filière pour lui donner une forme spécifique. Ce processus permet de produire des profils complexes tels que des joints d’étanchéité de différentes formes, des tubes de différents diamètres, ou des bandes pour diverses applications, notamment dans l’automobile, la construction et l’aéronautique.
Types de profils extrudés en caoutchouc
- Profils mono-matière : Profils fabriqués à partir d’un seul type de caoutchouc, souvent utilisés pour des applications standard d’étanchéité.
- Profils bi-matière : Ces profils combinent deux matériaux pour offrir des propriétés distinctes avec par exemple un matériau compact pour la pince et un matériau cellulaire pour le bulbe afin d’apporter une meilleure résistance à l’abrasion ou une meilleure étanchéité. Parfois, ils intègrent une insertion métallique, ce qui renforce la structure de la pince et permet une meilleure tenue du profil sur son support dans des environnements exigeants.
Caractéristiques et avantages du profil extrudé en caoutchouc
Les profils extrudés en caoutchouc peuvent être coupés à la longueur souhaitée et soudés aux extrémités à l’aide d’un outillage de vulcanisation pour former des joints sur mesure. Ce processus garantit des joints continus et hermétiques, adaptés aux exigences spécifiques de chaque client. La vulcanisation, essentielle à l’extrusion, consiste à chauffer et à presser le caoutchouc pour durcir et stabiliser le matériau, le rendant ainsi plus résistant aux contraintes thermiques et chimiques.
Applications et matériaux pour profils extrudés en caoutchouc
Les matériaux utilisés varient selon les besoins de l’application. Des caoutchoucs tels que l’EPDM, le néoprène, et le silicone sont couramment employés pour leurs propriétés spécifiques : résistance aux intempéries, isolation thermique, ou résistance aux produits chimiques. En fonction de l’usage (intérieur ou extérieur), ces matériaux doivent être choisis avec soin pour garantir la durabilité du produit fini.
Ce processus d’extrusion offre une grande flexibilité de conception et permet de créer des produits sur mesure, durables, et adaptés à des environnements extrêmes.
Moulage de pièce en caoutchouc
Le moulage du caoutchouc par compression et par injection sont deux méthodes utilisées pour fabriquer des pièces techniques, mais chacune a ses spécificités, avantages, et inconvénients en fonction des besoins du projet.
Moulage du caoutchouc par compression
Le moulage par compression consiste à placer le caoutchouc cru non durci (généralement préchauffé) directement dans les empreintes du moule ouvert. Une fois que le moule est refermé, de la chaleur et une pression élevée sont appliquées pour forcer le matériau à épouser la forme du moule. Ce processus est particulièrement adapté aux pièces simples et robustes, comme les joints et les composants nécessitant une bonne résistance thermique ou chimique.
1. Avantages du moulage caoutchouc par compression
- Faible coût de fabrication pour les grandes pièces simples
- Meilleure adaptation aux matériaux thermodurcissables qui résistent à la chaleur et à la déformation
- Moins de déchets en réutilisant les excédents de matériau
2. Inconvénients du moulage caoutchouc par compression
- Production plus lente due à des temps de cycle plus longs
- Limitations dans la complexité des détails, ce qui le rend moins adapté aux pièces très détaillées ou avec des géométries complexes
Moulage du caoutchouc par injection
Le moulage par injection est un processus plus automatisé et rapide, où le caoutchouc est fondu et injecté sous haute pression dans une cavité de moule fermée. Il est idéal pour les pièces plus complexes et pour les productions en série, car il permet de créer des pièces très détaillées avec des tolérances serrées.
1. Avantages du moulage caoutchouc par injection
- Précision élevée et capacité à produire des pièces complexes avec des détails fins.
- Temps de cycle rapide, ce qui favorise une production de grande série.
- Moins de déchets, car le processus est plus optimisé et génère moins de matière excédentaire.
2. Inconvénients du moulage caoutchouc par injection
- Coûts d’outillage plus élevés, car chaque nouveau moule nécessite un nouvel outil, ce qui peut entraîner des délais et des coûts supplémentaires.
- Matériaux plus coûteux, notamment lorsque des thermoplastiques ou des caoutchoucs spécifiques sont utilisés.
Quelle technique choisir entre le moulage du caoutchouc par compression et le moulage du caoutchouc par extrusion ?
Le choix entre moulage par compression et moulage par injection dépend de plusieurs facteurs, notamment le volume de production, la complexité des pièces, les tolérances nécessaires, et les coûts liés aux matériaux et à l’outillage. Le moulage par compression convient mieux aux grandes pièces simples et robustes, tandis que le moulage par injection est plus adapté aux productions en série nécessitant une grande précision et des pièces détaillées.